Between them, Titleist's Brian Comeau (left) and Derek Ladd (right) have been granted over 700 patents related to the golf ball.
At Titleist we devote a great deal of time to speaking with golfers – finding out what's important to your game and how we can create products that will help you play better and enjoy the game more. It's a perpetual cycle of give-and-take that helps us to constantly improve. We have these conversations with golfers of every shape and size, men and women, juniors and seniors, people just starting to take up golf as well as the most accomplished and highly skilled players in the world.
Consistency Matters
Throughout all of these discussions one theme has continually surfaced – Consistency. We've heard, loud and clear and across the wide spectrum of golfers, that consistency matters when it comes to their golf ball. In fact, in a recent Forum poll question, Team Titleist members ranked consistency as the most important aspect of golf ball performance.
But consistency can mean very different things to different golfers. Some measure consistency around the green - how reliably a golf ball spins and checks up on chips and pitches. For others, as we learned in a recent Q&A article with Justin Thomas, distance control and how well a golf ball flies through an expected trajectory window are top priorities. But when we dug a little deeper into the subject, we found that for half of all Team Titleist golfers polled, consistency means:

•••

Making the Most Consistent Ball in Golf
The challenges of making a product that feels, flies, spins and sounds the same from golf ball to golf ball falls on the shoulders of the Titleist Golf Ball Research and Development team. When you think of the role that R&D plays, you'd probably credit this group with designing new golf ball models and making improvements for new generations of existing models. And you'd be absolutely correct.
But it's only half of the story.
Once R&D has created a final prototype golf ball that meets all the desired performance and quality specifications, Titleist scientists, engineers and technicians turn their attention to the task of replicating that successful ideal on a mass scale. It's no small feat, as we learned during a recent visit behind the card-access walls of Titleist Golf Ball R&D.
Mass production of Titleist golf balls involves hundreds of tightly monitored steps in a precision process that transforms a mix of raw materials into products that defy doubt.
As Derek Ladd, Senior Project Manager of Research & Intellectual Property told us, "Pro V1 and Pro V1x are the most trusted golf balls in the world for two reasons. The first reason is the unparalleled level of performance they deliver. There are no holes. They excel in every phase of the game. Pro V1 and Pro V1x are long off the tee, they offer precise distance control and very tight dispersion patterns on iron shots and they provide exceptional spin and soft feel in the short game."
And reason number two, we asked?
"Have you ever hit a bad one?"
To Derek's point, golfers' faith in the golf ball really only runs as deep as the last ball teed up. If, for any reason, that ball flew shorter, or off-line, or if it spun more or less, or it felt harder or softer than the ball we played the previous time out, that trust would quickly erode. This is why Golf Ball R&D keeps their finger on the pulse of every step in the manufacturing process and why we also have a dedicated R&D and Quality lab within our Ball Plant 3 facility in New Bedford, MA (where we make Pro V1, Pro V1x and AVX golf balls).
There is a direct correlation between manufacturing and product consistency and consistent performance on the golf course. It's a source of pride for both Golf Ball R&D and our Manufacturing teams. In fact, if you attend a tour of our Ball Plant 3 operations, there's a sign at the final x-ray inspection station that relays a remarkable fact: less than one Titleist golf ball in 10 million is returned for replacement due to manufacturing error.
•••
Nick Nardacci, Senior Manager of Research Engineering, examines the dimples on a batch of prototype golf balls in the Titleist Golf Ball R&D lab.
How R&D Defines Consistency
So, what are some of the challenges in trying to make golf balls that are virtually identical to one another? To find out, we met with Brian Comeau, Director of Materials Research at Titleist. As Brian explained, the challenges are as numerous and as varied as the hundreds of steps required to make a Pro V1 or Pro V1x golf ball. But from R&D's point of view, the challenges fall into one of two categories – Chemical or Mechanical.
"When we talk about chemical considerations," Brian explained, "one aspect of the process that we're talking about is formulation – the mixing of raw compounds to make golf ball materials. Just like in cooking, you have to start with the right ingredients for each component of the golf ball's construction – core, casing layer and cover. Those ingredients have to be combined in precise proportions, conditioned and cured to exact specifications. Each time we "cook" these separate parts of the golf ball, we have to follow the recipe exactly. Then we test them to double check everything was made right.
On the mechanical side, we're talking about construction, the physical assembly of the different layers. To do this properly, we have to develop a series of precise processes with strict timing between each step. The instruments and machines used in assembly are precision tooled and we mobilize a staff of dedicated technicians to test and monitor every mechanism from start to finish. So in the chemical phase, we're forming the building blocks. In the mechanical phase, we're putting those blocks together to create a finished golf ball. In both phases, chemical and mechanical, we have to function the same way every time. Otherwise, the characteristics of golf ball performance change."
•••

How Inconsistency Can Effect Golf Ball Performance
So where are some of the pitfalls that R&D faces and how do they address those challenges?
"Within Golf Ball R&D we talk a lot about 'The Process'," Derek Ladd said. "Process Excellence was a founding principle of the Acushnet Company and it's still a main pillar that guides us today. It's like a playbook that we all follow. It defines every step, every detail, every safeguard in making the golf ball. A key part of the process is constantly anticipating 'What can go wrong?' and heading off potential problems before they can occur. The consistency we achieve in the final product owes a lot to that mindset."
Just to play Devil's Advocate, we wanted to know what would happen if something didn't go according to plan in the manufacturing process. If the core materials of a Pro V1 were mixed out of proportion, or if the paint on a Pro V1x's cover was applied too thickly, what would we see if we took that ball to the golf course? Derek and Brian outlined a few scenarios for us:
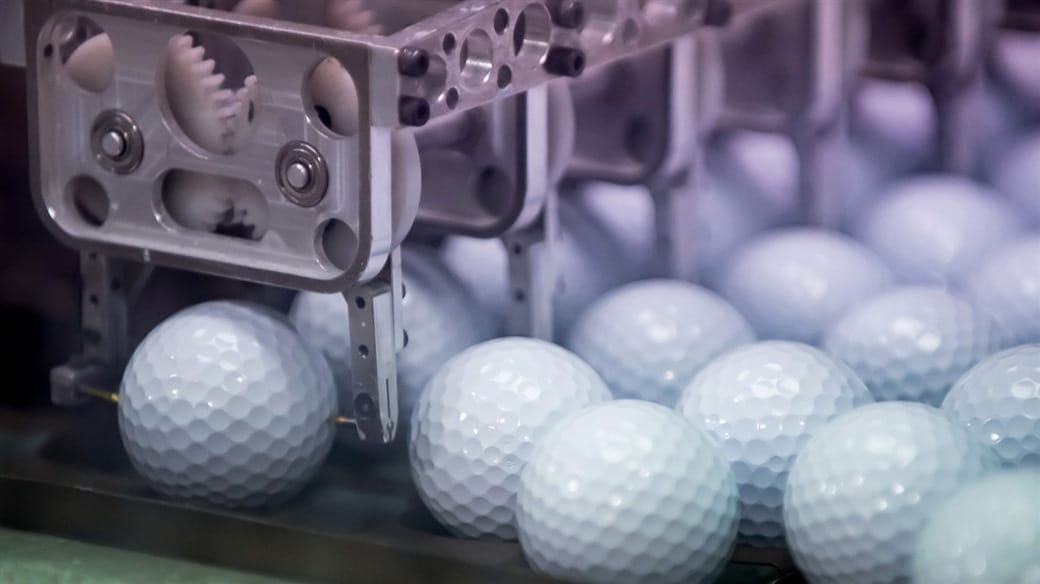
Chemical Challenges to Consistency
Sourcing
The quality of the raw materials used, and the manner in which they are stored and served to manufacturing is crucial. If, for some reason, we used an inferior polybutadiene (the synthetic polymer rubber material that is the chief ingredient in the golf ball core) it's likely that that material wouldn't meet our standards for resilience. A material that is resilient means that it recovers quickly when a stress is applied to it (such as an impact with a golf club). This quality is what makes the core fast and what makes the Pro V1 and Pro V1x fly so far off the tee. If you were to play a ball with inferior materials in the core, you'd likely see a noticeable drop in distance.
Fortunately, every shipment of polybutadiene (and all raw materials) that we use is tested and verified by our partner vendors prior to shipment. We test the materials again once it arrives at Ball Plant 3.
Mixing
The accuracy, timing and quality control in the levels of ingredients for each material is also critical. For example, in core construction, we use zinc diacrylate, a chemical component that generates a high level of cross-linking among the long polybutadiene molecules. The more that the molecules are linked, the stronger the chemical bonds and the faster (more resilient) the core will be. However, in core formulation we have to strike a balance between high resiliency (lots of cross-linking) and compression.
Generally speaking, more resilient (fast) cores are harder. So if we were to use too much zinc diacrylate, the result could be a golf ball with an extremely hard core. On the course, that golf ball would produce a harsh sound and a "clicky" feel at impact. It could be especially troubling in the short game, where you rely so much on consistent feel and sound to judge the weight of your shots.
To make sure this doesn't happen, after mixing, every batch of core material is tested for physical properties such as compression and if a batch was out of specifications in any test, the batch in question would be taken out of production and destroyed.
Curing
Consistent temperature during curing is as essential in golf ball manufacturing as the temperature of an oven is in cooking. It plays a significant role in the quality and consistency of the cross-linking of polymers to form the final parts or layers. If the temperature during compression molding of the core is not uniform across the press, or if the temperature of one press is different from another, the result will be inconsistent size, weight and/or compression. You'll end up with golf balls that fly, feel and spin completely differently.
Consistency in curing is also critical during the cover application. Once finished, golf ball cased cores are transported to cover operations, where they are warmed in insulated ovens to specific temperatures. They are fed directly onto an assembly line where they are cast in thermoset elastomer urethane, which is mixed and applied as a liquid around each core. The urethane covered cased cores are maintained at a specific curing temperature, ensuring that the cover forms a tough, uniform layer around the core at the desired hardness. If the initial temperature of the finished core was not warm enough, or if the time the covered core spent curing was too short or too long, you could see inferior durability on the golf course. If the cover doesn't adhere properly to the core, the cover could slip when struck by a golf club, essentially bunching up along the surface of the core. If the force is great enough, the cover will shear or even slice open.
To head off this potential problem, , technicians closely monitor the temperature of warming ovens, finished cores, and the mixed urethane. As part of Titleist's QA procedures, finished golf balls are tested every day for durability.
•••
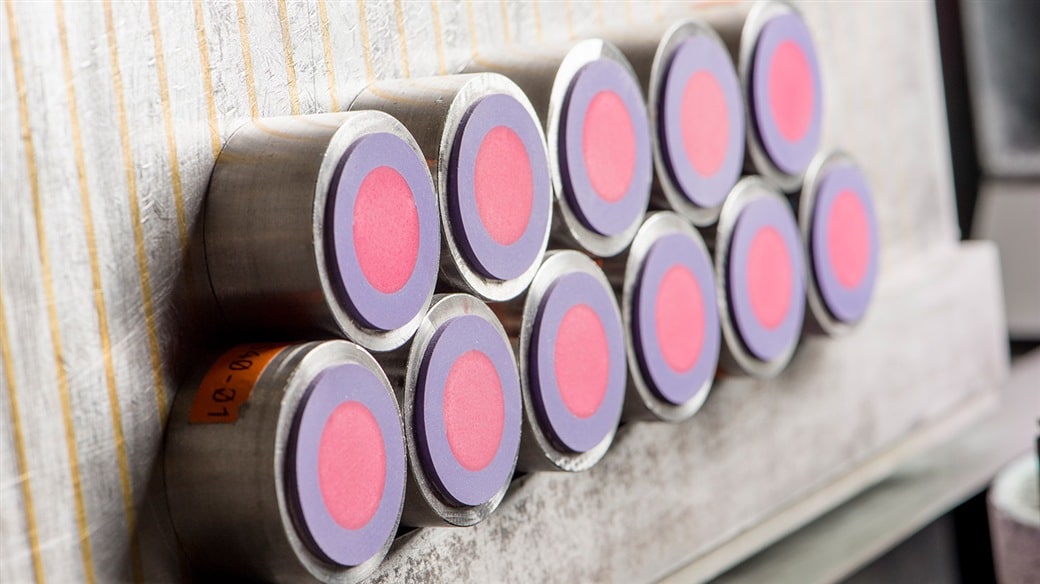
Mechanical Challenges to Consistency
Precision Tooling
The instruments and machinery used in manufacturing must be constantly monitored and maintained to ensure that every piece of equipment is operating properly and within strict tolerances. This oversight takes place from the beginning of the process, with our three-story gravity-fed rubber mixer that we use to mix and prepare golf ball core materials, all the way down the line to our hobbing process, in which Titleist machinists form the cavities that are used to cast the covers for Pro V1 and Pro V1x. Scales and sensors also have to be closely monitored and calibrated, to ensure that material weights and proportions, temperatures and timed cycles are always consistent.
What would happen, for instance, if settings were off in our Glebar operation? Glebar is a wet-grinding process that we use to grind molded cores to precise diameters. Let's say that we've just applied a Surlyn casing layer to a batch of Pro V1x dual cores. They're transported to Glebar, where somehow the specified grinding thickness is off. The main purpose of the casing layer is to protect the core from moisture absorption, which can ruin the core's resilience and the performance of the ball. However, the casing layer also serves a performance function. Because it's made with a resilient ionomer material, it can increase ball speed as well as modify the ball's spin profile.
If a ball came out of Glebar operations with too thick a casing layer, the ball would feel significantly harder in play than you'd expect. It would likely not spin as much either, so you might find yourself scratching your head at shots that seemingly fall out the sky or have more run out around the green.
To prevent this, as finished cores come out of Glebar, they must pass through two sets of steel gauges that prevent any cores from continuing on that don't meet the proper specification for finished diameter. This check is implemented after all core molding as well as after casing layer application.
Uniformity
Synonymous with consistency, uniformity is a term we use frequently in R&D to include the order, timing and recipe of each batch in the construction process. If any step in the process isn't uniform, the result will be inconsistent physical properties in the finished product. And inconsistent finished products perform differently, something you don't want to see on the golf course.
One process stage that we have to pay very close attention to is in paint operations. You might not give it much thought, but paint can have a dramatic influence on golf ball aerodynamics. For example, what would happen if we applied too thick a layer of paint to the cover of a Pro V1? The short answer is it wouldn't fly like a Pro V1. If too much paint is sprayed on the cover, it pools in the dimples. This effectively changes the shape and depth of the dimples that Titleist aerodynamicists originally designed. With too much paint, the dimples become effectively shallower. Shallow dimples result in lower flight, so out on the golf course you might wonder why you suddenly can't elevate your shots the way you're used to.
Fortunately, our paint sprayers are closely monitored for both duration of spray interval, volume of paint applied per spray, and uniformity. Technicians clean and replace spray heads according to a strict schedule and painted balls are hand-inspected as an important QA check.
Concentricity
The accuracy of the construction, particularly its concentricity (centeredness of the layers) is a huge concern, because it has such a profound effect on performance. If the golf ball inner core is just 40/1,000 of an inch off-center (a hair more than the thickness of an average credit card), shot dispersion can double! That goes for a drive swung at 120 mph all the way down to a 15-foot chip shot.
Concentricity is particularly challenging in making dual-core constructions, like Pro V1x. To make a dual core, a small inner core must be placed between two outer core shells in a core mold press. This assembly is then heated under pressure at a precise temperature and for an exact period of time. When done preoperly, the result is a dual core that is perfectly crosslinked and centered. But let's suppose the shells were not precisely formed. This could potentially result in the inner core shifting slightly within the outer core as it bakes.
If this core proceeds to casing, cover and paint operations, you'll be teeing up a ball with an off-center core. Depending on how the “thick” side of the ball is oriented, you could put a perfect swing on the ball and it could fly left or right, short or long, low or high.
Understanding the importance of concentricity, our core molding process is systemically regulated and monitored. Each molding press is calibrated and heating times are fully automated. Finished dual cores are dissected and examined by plant technicians throughout every production shift to ensure that cores meet our demanding tolerances for core centeredness, the most stringent in the golf industry.
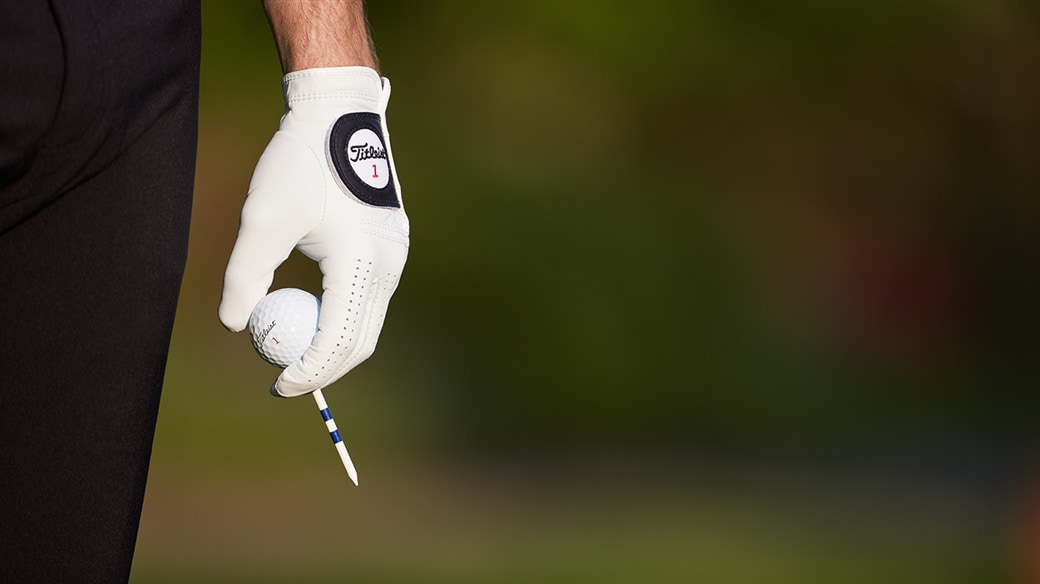
•••
Thanks for the science lesson, Derek and Brian! And thanks for all you do to make the most consistent golf balls in the game.
#TeamTitleist